Here's How Dow is Addressing the Chemical Industry's Digital Transformation Lag
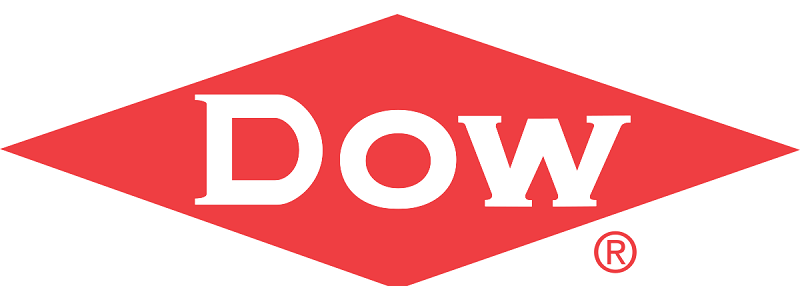
Digital transformation is helping brands all over the world bring exciting new technology into their business models. Whether it’s using augmented reality or beacons to create amazing customer experiences, or automation and artificial intelligence on the backend, streamlining processes and eliminating inefficiencies, there is almost unlimited scope for innovation when it comes to digital transformation.
However, some industries are lagging behind others when it comes to their digital transformation. This may be because it’s more difficult to work digital technology into a particular industry’s operations, or it could be that the industry in question is one which is too reliant on and committed to more traditional processes and practices. Whatever the reason, it’s important that these lagging industries get with the digital transformation programme, lest they find themselves stuck too firmly in the past while the rest of the world speeds into the future.
The chemical industry is one such arena, and Dow is doing its best to address its own digital transformation lag.
Dow Chemical Company
While research suggests that 75% of chemical (and other businesses operating within the process industry) companies are actively participating in digital transformation and making attempts to bring Industry 4.0 technology into their fold, less than 25% are moving beyond the pilot phase.
This condition is not uncommon in digital transformation and even has a term associated with it – pilot purgatory. Many industries find it difficult to take digital technology from the testing stage and roll it out across their operations, and companies which can crack this particular nut are rewarded with the benefits such technology can offer their brands.
There are many challenges facing the chemical industry when it comes to trying to implement digital transformation. It can be difficult to justify investment to executives when there are so few proof of concept cases to present. A lack of seamless integration and conflicting organisational design issues around technology and IT solutions. Cybersecurity issues, the need for updated training, the capture of tribal knowledge, siloed information, and more are all standing in the way of chemical brands making a real success of their digital transformations.
Asset utilisation is one of the most pressing issues in the industry right now and it’s one which can be greatly improved by Industry 4.0 technology. However, because it doesn’t generate savings or revenue for the business on its own, it can still be a tough sell to the people holding the purse strings.
Digital Transformation
When Dow first began its digital transformation, it was searching for a way to improve the vertical integration between the enterprise and shop floor arms of the business. This involved identifying where technology could address the gaps between its enterprise solutions and floor assets.
The main obstacle to – and simultaneously the motivation for – digital transformation was the fact that Dow had a significant number of legacy machines and systems coming to the end of their useful life as they were no longer compatible with the updated ERP solutions.
“One of the key learnings from the programme was the barrier of reinvestment cost,” said MES Global Improvement Leader at Dow Chemical, Angela Morris. “The solution required incremental value creation with phased reinvestment to be successful. Given the technology constraints at the time and existing architectural compatibility issues, the full value of vertical integration was not realised – so, the programme was placed on hold.”
Now, in 2019, the landscape has changed, and Dow is in a place to make the most of Industry 4.0 technology, while still drawing useful function from those legacy systems which can still be of benefit.
“Much of the front-end analysis of functional requirements derived and economic justification have been leveraged into a restructured effort under the Industry 4.0 banner using new breakthrough technologies such as virtualisation and analytics,” continued Morris. “The MES installed base is now being repositioned for duty as edge services supporting enterprise-based real-time execution applications.”
Legacy systems can help Industry 4.0 applications with the real-time performance indicators they require to justify their existence in the chemical industry. By creating a bridge between the realities of the currently installed base to the brave new world of digital transformation, these legacy systems can help brands break free of pilot purgatory.
Final Thoughts
The chemical industry is lagging behind in digital transformation. However, by leveraging the power of legacy systems, brands such as Dow can bring new B2B solutions to the shop floor with digital technology – simultaneously boosting revenue and efficiencies.
“It is not economically feasible for companies such as Dow Chemical to “rip and replace” the still-functioning legacy systems, so an incremental migration path approach is needed,” concludes Morris. “It is important to integrate but maintain flexibility and scalability. MES architecture and associated functionality must evolve over time, as its mission and functions change.”
You can hear Dow’s Global Marketing & Customer Experience Director, Carlos Silva speak at B2B Online Europe 2019, being held in November at the Hesperia Tower Hotel & Convention Centre, Barcelona.
Please download the agenda today for more information and insights.